Digital Machining
Y. Altintas, Ph.D., Dr. Cau-Budapest, Hon.Dr. Ing. (Stuttgart)
Fellow of Royal Society of Canada, EC, CAE, CIRP, ASME, SME, ISNM, P&WC, Tokyo Univ.
NSERC – P&WC Industrial Research Chair Professor in Virtual Machining
|
|
Abstract
The aim of our research is to develop mathematical models of metal cutting operations, machine tool vibrations and control. The science based digital models allow the virtual design of machine tools, and testing and optimization of machining operations.
The model predicts the cutting forces, torque and power consumed in machining parts by considering material properties, cutter geometry, structural flexibilities, and cutting conditions along the tool path. The structural dynamics of the machine tool can either be imported from Finite Element analysis if the machine tool is at the design stage, or from the experimental modal measurements if the machine is already built. The simulation system predicts chatter free cutting conditions within the work volume of the machine tool, or detects the presence of chatter vibrations along the tool path. The dynamics of servo drive control systems, and trajectory generation as a function of jerk, acceleration and velocity profiles of machine tools are considered in simulating the machine tool behavior. An in-house developed virtual and real time CNC system allows the design and analysis of any five axis machine tool controller.
The algorithms are published in open literature (Google Scholar h-68 with over 16400 citations), and packaged in industrial software tool box which can be used as a process planning tool by production engineers or as an analysis module by machine tool builders (over 200 companies and research centers world-wide). We are currently developing a controller for a 9 axis precision micro machine built in our laboratory, investigating damping of machine tool vibrations, and the stability of turning, drilling, boring, micro-cutting, threading of pipes and mill turn operations.
|
|
Developments and Challenges in Machine Tools
Christian Brecher Dr.-Ing.
Ordinary Professor for Machine Tools at the Laboratory for Machine Tools and Production Engineering (WZL) of the RWTH Aachen
Director of the Department for Production Machines at the Fraunhofer Institute for Production Technology IPT
|
|
Abstract.
The accurate simulation and prediction of machine tool characteristics still remains a challenge. New methods for precise estimation of damping ratios are supplemented by substructure coupling and provide an approach for accurate prediction of machine tool dynamics due to structural modifications in the development and prototyping phase. In addition, also thermal aspects and the development of calculation methods will be discussed.
Additive manufacturing and integrated information technologies offer a multitude of opportunities and challenges for enhancing the functionality of conventional machine tools. For example, selective laser melting can be used to develop structural devices with complex geometries. The combination of conventional and additive manufacturing may enable a paradigm shift from rapid prototyping to rapid manufacturing. The safety measures for the operator and machine are of major importance.
This presentation provides an overview of the current trends in the development and simulation of conventional machine tools as well as the contemporary research in the field of integration of laser assistance, additive manufacturing, process data feedback and cloud based optimization in machine tools.
Keywords: Damping, Dynamic Substructuring, Additive Manufacturing, Integrated
Technologies, Process Data Feedback |
|
Cloud-Based Design and Additive Manufacturing of Custom Orthoses
Albert J. Shih Ph.D.
Fellow of ASME, SME, Associated member of CIRP
Professor, Mechanical Engineering, Professor, Biomedical Engineering, Associate Chair, Integrative Systems + Design, Director, Global Automotive and Manufacturing Engineering, Univ. of Michigan at Ann Arbor
|
3001E EECS
University of Michigan
2350 Hayward St.
Ann Arbor, MI48109-2136 , USA
shiha@umich.edu
|
![clip_image002[11] clip_image002[11]](http://vmpt2016.conf.tw/site/userdata/1089/wlw/KEYNOTE-SPEAKER_A103/clip_image002%5B11%5D_1.jpg)
|
|
Abstract
Advancements in virtual manufacturing that impacts the patient care of custom orthoses are presented. Orthoses, also known as braces, are assistive devices for structural support of the neuromuscular and musculoskeletal systems to help people with impairments to regain their mobility and independent living. Custom orthoses has personalized fit, better comfort, and superior efficacy in treatment than pre-fabricated ones for users. Unlike factory with engineers on-site, the digital design and manufacturing are challenges in the hospital setting. This talk presents a cyber-physical manufacturing system at the University of Michigan Orthotic and Prosthetic Center (UMOPC) with cloud-based design and additive manufacturing (AM) of the ankle-foot orthosis (AFO). The fabrication time and material cost for AM are critical to provide advantages over the conventional methods for fabrication. This system targets to achieve the one-day visit for stroke patients who need AFO. Key elements of the manufacturing system presented in this talk include the: (1) digital scanning of the foot and leg, (2) CAD software for process and exchange the surface and solid .STL files, (3) web-portal for clinician and design engineer, (4) wavy structure tool path planning for AFO, (5) fused deposition modeling (FDM) of carbon fiber in Nylon for hard structural and soft silicone for wearable assistive devices, and (6) inertia measurement unit (IMU) for gait analysis and monitoring of users. Measurement techniques for evaluation and quality control are presented. Expansion of this manufacturing system for prosthetic socket, foot orthoses, and other assistive devices are elaborated. Altogether, the cyber-physical service system (CPSS) features the one-day delivery, passive dynamics for personal needs, long-term monitoring using the IMU for custom assistive devices and demonstrate the potential societal impacts enabled by the virtual manufacturing of personalized products.
|
|
How University Research Supports the Technological Development of Modern Machine Tools
Michael F. Zaeh Dr.-Ing
Memberships of acatech, WGP, WLT, CIRP (associated mamber)
Full Professor for machine tools and manufacturing technology at Technische Universitaet Muenchen
|
Institute for Machine Tools and
Industrial Management (iwb),
Technical University of Munich,
Boltzmannstrasse 15, 85748 Garching, Germany
Michael.zaeh@iwb.tum.de |
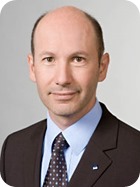
|
|
Abstract
Modern machine tools incorporate a multitude of new functions and new features. New mechanical structures evolve and in some areas robots are replacing classical machine tools. However, generally spoken, the classical serial mechanical design of machine tools is still widely used. The technological development brings up changes more in detail. Modern machine tools shape a platform for hybrid processes, they allow the shortening of process chains, they are advanced in terms of their dynamic behavior and damping, they use adaptronic functions, they are thermally stable, they allow for multiple technologies, they are resource efficient and environmentally friendly and they are developed by using sophisticated means of simulation. The consumption of electrical of machine tools is also coming into the focus of research, in particular in Germany, where the transition to a mainly regenerative power supply is on its way. This presentation outlines these trends and uses examples out of the author´s fields of research and interests.
Key words: Machine tool structures, mechatronics, multi technology platform.
|